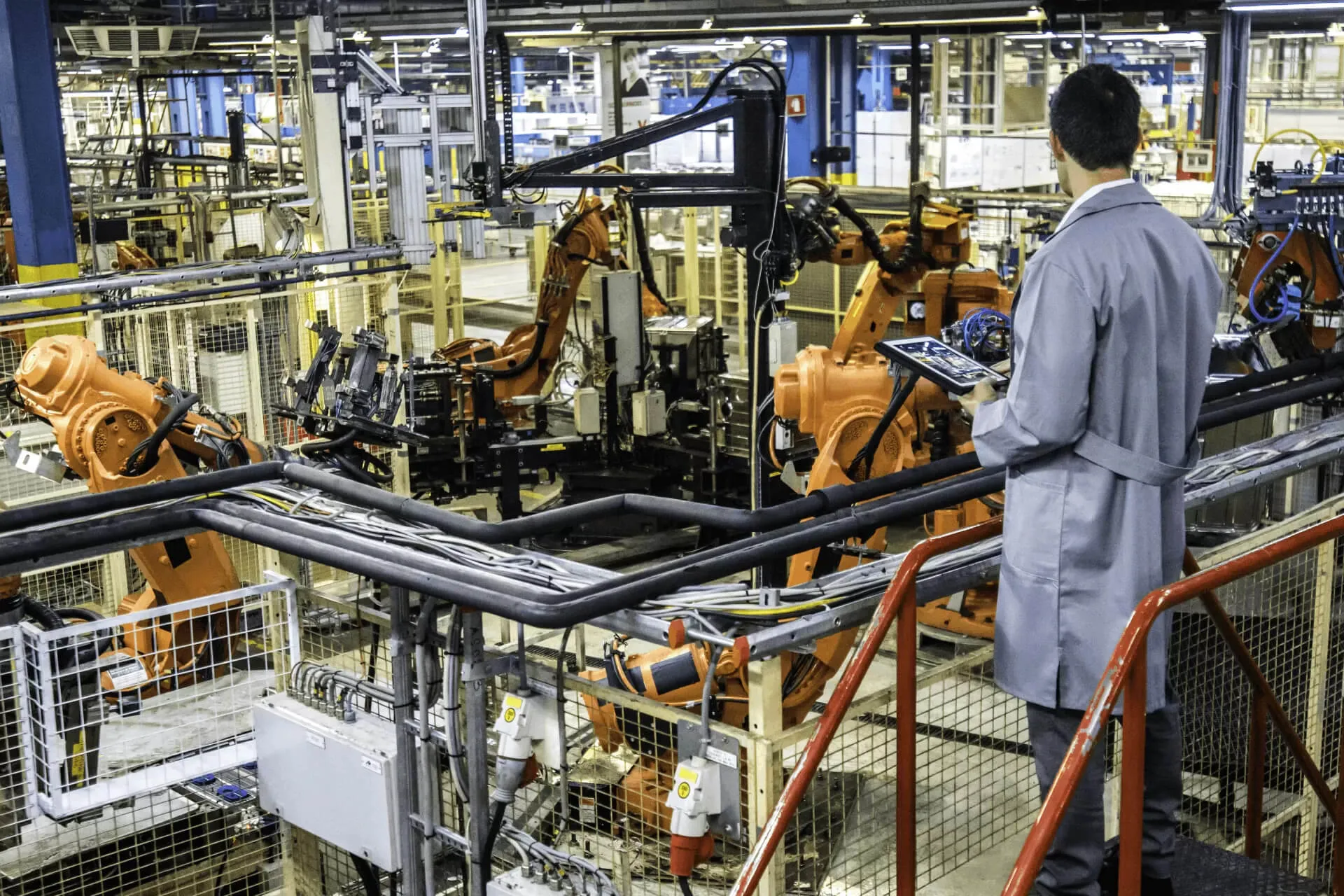
Connected Operations – The First Step in Your IoT Journey
Connectivity is not a new concept within the manufacturing domain. Manufacturers have traditionally leveraged the cloud to transform the shop floor into a smart factory, analyze real-time data, and support data-driven decision-making processes. However, with industry 4.0 adoption, connected operations have become a crucial differentiator.
Connected operations leverage digital technologies across the value chain - product development, manufacturing, operations, supply chain, and service. A connected enterprise is formed by connecting these stages, resulting in the unity and integration of information technology (IT) and operational technology (OT), leading to a digital thread of information that spans the entire value chain.
Connected operations deliver significant benefits such as faster time to market, increased productivity, reduced machine downtime, better asset utilization, enhanced energy efficiency, improved overall equipment effectiveness (OEE), etc.
Some impacts of connected operations on manufacturing processes include:
-
Manufacturing operations: Advanced planning and scheduling using real-time production and inventory data to minimize waste and cycle time.
-
Inventory tracking: Sensors to track real-time movements and locations of raw materials, work-in-progress and finished goods, and high-value tooling.
-
Quality: Real-time equipment monitoring to predict potential quality issues.
-
Maintenance: Augmented reality to assist maintenance personnel in maintaining and repairing equipment.
-
Environmental, health, and safety: Sensors to geofence dangerous equipment operating near personnel.
IoT challenge for connected operations
IoT-enabled connected operations is a fast-emerging opportunity for hi-tech and manufacturing companies. However, along with the new business model and opportunities come new challenges. Companies that adopt IoT technology face managing disconnected systems and data silos. With IoT data stuck in systems separate from the rest of the business, teams deal with complicated processes across multiple systems. As a result, companies cannot realize the total value of their IoT devices, leaving potential insights on the table. They are stuck with less efficient processes and missed opportunities to boost customer satisfaction.
The first step in your IoT journey is to get “things” connected
Most companies don’t understand where to start their IoT journey. The first step is to start with your existing devices. Some of these may be connected to incompatible networks or may not be connected. Start by getting these devices across a single enterprise-wide network and adjusting the existing business processes to take advantage of the data flowing through the shared network. Such connected operations will start realizing benefits immediately.
A Cisco study showed that connected digital technology could spur an 11 percent bottom-line improvement for oil and gas companies. We can save billions of dollars and avoid environmental damage if devices on an oil rig can be connected through sensors at appropriate spots, making a networked data platform. The operators can even warn about a potential oil well blowout before it happens by analyzing the data.
Real-time > predictive > autonomous
As technology develops, connected operations will move beyond providing just real-time data to manufacturing organizations. It will have embedded predictive analytics capabilities and provide a true autonomous production environment where production equipment can make decisions independent of human intervention in the context of real business conditions and objectives.
Connected operations to enable customers to thrive and innovate with software faster
Connected operations go beyond simplifying the complexity using connected edge, IoT, and cloud. At Zensar, we also focus on providing our customers with a connected modern experience. We make every customer interaction matter by connecting all business data across advertising, enterprise resource planning, marketing, sales, commerce, and service to deliver exceptional customer experiences. We offer connected engineering to accelerate your ROI by enabling you to develop and deploy superior business software faster.
At Zensar, we not only empower you to build a connected future but also focus on energizing your core and innovating at scale, thus helping you drive business resilience.
Zensar’s reference architecture for “connected operations” is the convergence of the application of the Internet of Things, the use of advanced robotics, and the application of advanced analytics of big data in supply chain management: place sensors in everything, create networks everywhere, automate anything, and analyze everything to significantly improve performance and customer satisfaction
Our Connect Operations playbook is the key enabler of the digitization of the supply chain which in turn helps our customers to address the new req , the challenges on the supply side as well as the remaining expectations in efficiency improvement.
Zensar’s Connected Operations brings about a Supply Chain 4.0, which will be ... Agile, Intelligent, Adaptive and Accurate
Our case studies and market research suggest that the potential impact of Connected Operations in the next two to three years is huge – up to 50 percent lower operational costs and a reduction of 75 percent in lost sales while decreasing inventories by up to 50 percent are expected, at the same time increasing the agility of the supply chains significantly.